For jewelry casting, manufacturers have a wide range of base metals and alloys to select from for their pieces. Most common metals that consumers are familiar with are gold, silver, platinum, and sterling silver. Yet there are many other types of alloys that may be used, including tin and zinc. When determining which alloy to select, here are several advantages to keep in mind when it comes to tin vs zinc alloys.
About Tin Alloys for Jewelry Casting
Tin alloys are commonly used in jewelry making, although they often go by different names. Pewter, Britannia, and Levalloy contain from 60% up to 92% tin along with lower amounts of antimony, copper, and cadmium. While some tin alloys used to contain lead, many metal manufacturers now offer lead-free alloys for jewelry casting to avoid the lead’s harmful effects on people’s health.
Tin alloys have very good to excellent fluidity as well as high tensile strength. The alloy also has good ductility and corrosion resistance. It may be used for intricate shapes, textured surfaces, thin walls, and for making ornate filigrees. Tin alloys could also be used for plating other metals used for jewelry, yet certain tin castings using Britannia does not need be plated. Tin alloys make the casting process easier due to having a lower temperature range from 475°F to 750°F.
About Zinc Alloys for Jewelry Casting
Zinc is often found in many alloys used for jewelry and art castings, such as brass and silver nickel. When zinc is the main base metal at 88% to 96%, it is commonly alloyed with copper and aluminum to make Zinc 995, Superdie I, and ILZRO-12. Zinc alloys may also contain nickel, which can cause an allergic reaction, and lead that is toxic. However, lead-free and nickel-free zinc alloys may be available for jewelry castings.
Zinc alloys have fair to good fluidity and extremely good tensile strength. It also has good corrosion resistance. The ductility of zinc varies based on the alloy, as Superdie I has very good ductility and ILZRO-12 has fair ductility but Zinc-995 has below average. So its lower malleability may cause problems. Zinc alloys are commonly used for thin walls and fine details for jewelry castings. This alloy requires a higher casting temperature at 735°F to 875°F.
Tin Alloys vs Zinc Alloys
Both tin alloys and zinc alloys may be used for jewelry casting. Yet when deciding between the two metals, tin alloys offers higher ductility and fluidity for castings. Tin alloys also may be cast at lower temperatures while casting detailed jewelry products. Here at Belmont Metals, we offer a range of tin, zinc and led-free alloys that may be used for jewelry casting. Contact our company today to learn more about the metals that we offer.
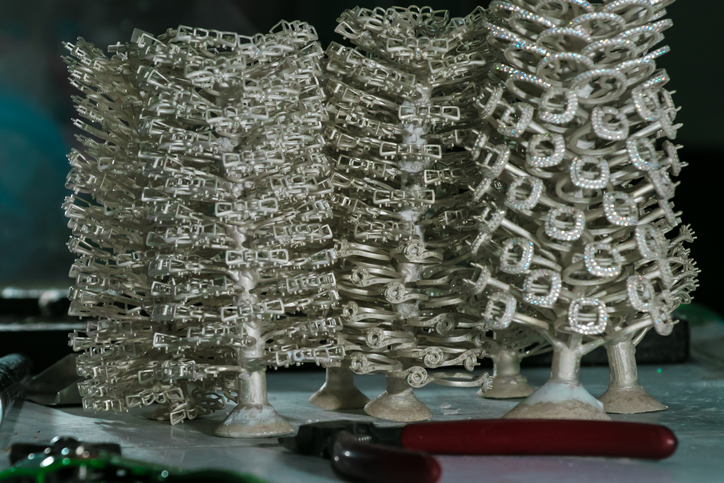